Understanding Bang Casting: A Comprehensive Guide
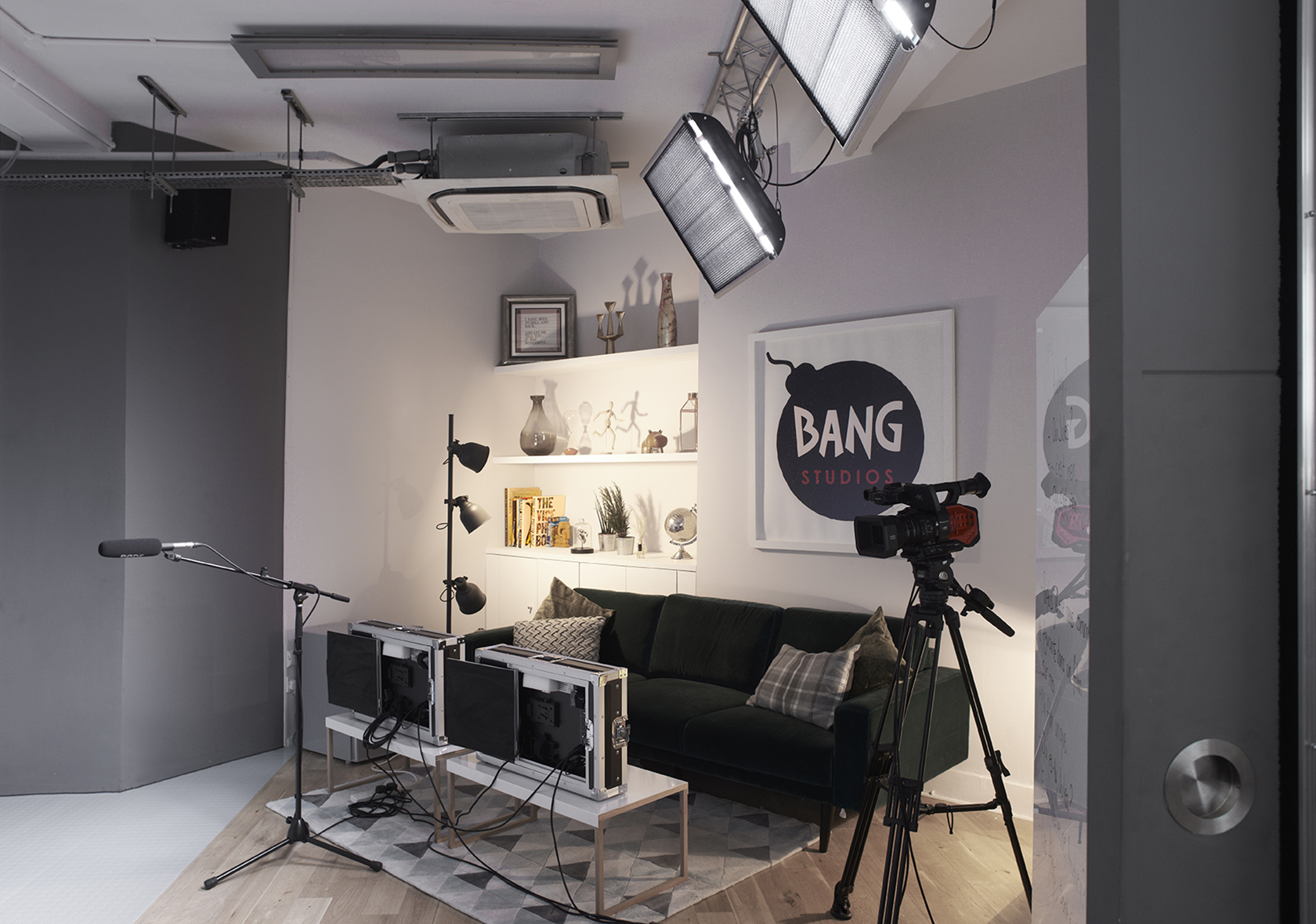
Bang casting is a crucial aspect of various industries, particularly in manufacturing and engineering. This article aims to provide an in-depth understanding of what bang casting is, its processes, applications, and its significance in modern production. With the rise of technology and innovation, understanding the intricacies of bang casting can empower individuals and organizations to make informed decisions in their respective fields, enhancing efficiency and quality.
The term "bang casting" may not be familiar to everyone, but it plays a significant role in the production of numerous products that we encounter daily. From automotive parts to intricate machinery components, the bang casting process is central to creating durable and high-quality items. As we delve deeper into this topic, we will explore its history, various techniques, and the advantages it offers over traditional casting methods.
In this article, we will break down the concept of bang casting into manageable sections, ensuring that readers can easily grasp the essential elements of this manufacturing technique. Whether you are a student, a professional in the manufacturing sector, or simply curious about the topic, this guide will equip you with the knowledge required to understand bang casting comprehensively.
Table of Contents
What is Bang Casting?
Bang casting is a specialized manufacturing process that involves the creation of metal components through a combination of force and heat. This technique is primarily used to produce parts that require high precision and durability. The process typically involves pouring molten metal into a mold and applying a sudden force to shape the metal into the desired form. This method is particularly advantageous for creating complex shapes and designs that would be challenging to achieve through traditional casting methods.
Key Features of Bang Casting
- Precision: Bang casting allows for high accuracy in the dimensions of the final product.
- Versatility: The technique can be applied to various metals and alloys, making it suitable for multiple industries.
- Efficiency: The process reduces waste and enhances production speed compared to traditional casting.
History of Bang Casting
The origins of bang casting can be traced back to ancient civilizations that experimented with metalworking techniques. Over time, the process evolved, with significant advancements occurring during the Industrial Revolution. The demand for mass-produced metal components led to the refinement of bang casting methods, making them more efficient and reliable.
Throughout the 20th century, technological innovations further enhanced bang casting processes. The introduction of computer-aided design (CAD) and computer numerical control (CNC) machining allowed for precise mold creation and better control over the casting process, leading to higher quality products.
The Bang Casting Process
The bang casting process can be broken down into several key steps:
Advantages of Bang Casting
Bang casting offers several advantages over traditional casting methods, making it a popular choice in various industries:
- High Precision: The ability to create intricate shapes with tight tolerances is one of the primary benefits of bang casting.
- Reduced Waste: The process minimizes material waste, contributing to cost savings and environmental sustainability.
- Faster Production: Bang casting can significantly reduce production times, allowing for quicker turnaround on projects.
- Versatile Materials: It can be used with a wide range of metals, including aluminum, copper, and various alloys.
Applications of Bang Casting
Bang casting is utilized in various sectors, including:
- Aerospace: Production of lightweight and strong components for aircraft and spacecraft.
- Automotive: Manufacturing of engine parts, transmission components, and other critical automotive elements.
- Consumer Goods: Creation of durable and aesthetically pleasing products, such as cookware and decorative items.
Different Techniques in Bang Casting
There are several techniques associated with bang casting, each with its unique advantages:
1. Die Casting
Die casting involves forcing molten metal into a mold at high pressure. This technique is ideal for producing large quantities of parts with excellent surface finish and dimensional accuracy.
2. Sand Casting
Sand casting utilizes sand molds to create metal components. This method is versatile and cost-effective, making it suitable for small production runs and complex shapes.
3. Investment Casting
Investment casting, also known as lost-wax casting, involves creating a wax pattern that is coated with a ceramic shell. Once the shell is hardened, the wax is melted away, leaving a mold for pouring molten metal.
The Future of Bang Casting
The future of bang casting looks promising, with advancements in technology paving the way for new possibilities. Innovations such as 3D printing and automation are expected to enhance the efficiency and precision of the bang casting process. Additionally, as industries continue to prioritize sustainability, the reduction of waste and energy consumption in bang casting will be a focal point of development.
Conclusion
In summary, bang casting is an essential manufacturing process that offers numerous advantages in terms of precision, efficiency, and versatility. As industries evolve, understanding the intricacies of bang casting will be vital for professionals and organizations aiming to stay competitive. We encourage readers to share their thoughts, experiences, or questions regarding bang casting in the comments section below. For more insightful articles, feel free to explore our website further.
We hope this comprehensive guide to bang casting has provided you with valuable insights into this fascinating topic. Thank you for reading, and we look forward to seeing you again soon!
You Also Like
Cast Of Spy Kids: Armageddon - Meet The Stars Behind The AdventureExploring Scott Porter's Movies And TV Shows: A Comprehensive Guide
Red Descendants: Exploring The Legacy Of A Cultural Phenomenon
Choosing The Best Compact Double Stroller: A Comprehensive Guide
Where Was Dune Filmed: Exploring The Stunning Locations Of The Epic Sci-Fi Film
Article Recommendations
ncG1vNJzZmiZlKK2r3rBqKmdnaKhrq%2Bw0mespGaTpLpwtsimpLJsX5eur7OMnJisrJmjtG%2B006aj